Bringing ideas to life, one layer at a time
Metal 3D Printing
Direct Metal Laser Sintering (DMLS)
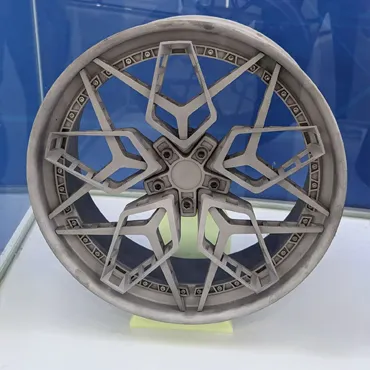
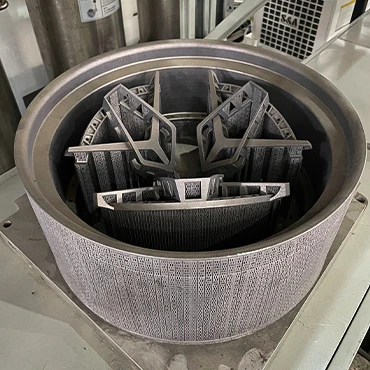
Materials
Aluminium-Silicon
Stainless Steel
Maragin Steel
Titanium
In718
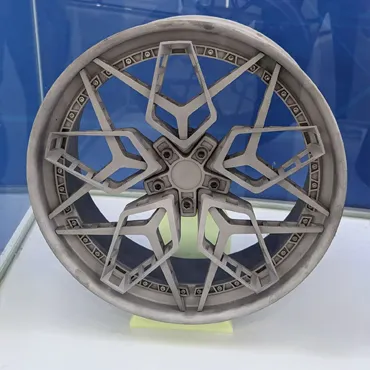
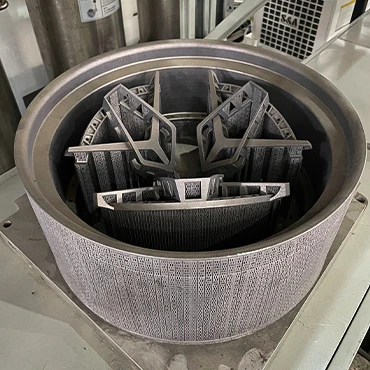
Process Flow :
Digital Design
A digital representation of the object is created using computer-aided design (CAD) software.
Slicing
Material Preparation
Printing
Layering
Post-Processing
Advantages :
Precision Engineering
Achieve precise and intricate designs with metal 3D printing technology, ensuring your components meet the highest standards of quality and accuracy.
Customization
Benefit from the freedom of customization, tailoring metal parts to your specific needs and designs for a wide range of industries.
Rapid Prototyping
Speed up your product development cycle with rapid prototyping, enabling quick iterations and design adjustments to bring your ideas to market faster.
Complex Geometries
Create components with complex geometries that are unattainable through traditional manufacturing processes, ensuring innovation and unique product designs.
Lightweight and Durable
Benefit from lightweight yet durable components, perfect for applications in aerospace, automotive, and other industries where performance matters.
On-Demand Production
Embrace on-demand production, reducing the need for large inventories and offering flexibility in manufacturing.
Sustainability
Embrace environmentally friendly manufacturing practices with reduced material waste and energy-efficient production methods.
Versatile Materials
Utilize a variety of metals such as maraging steel, titanium, and aluminum for a wide range of applications in multiple industries.
Personalization
Offer highly customized products tailored to individual customer needs, catering to the demands of a personalized market.
Innovative Additive Manufacturing Solutions by RIFTWAY SOLUTIONS
On-Demand manufacturing offers industries flexibility, cost reduction, customization, sustainability and simplifying the supply chain