Bringing ideas to life, one layer at a time
SLS (Selective Laser Sintering)
SLS
Selective Laser Sintering (SLS) is an advanced powder-based 3D printing technology that employs a high-powered laser to selectively fuse powdered materials, building objects layer by intricate layer. This process stands apart from traditional manufacturing techniques as it eliminates the need for molds or support structures. The absence of these constraints allows SLS to produce objects with complex geometries and exceptional precision. This capability is invaluable for applications requiring detailed and durable components, making SLS a preferred choice across various industries seeking efficiency and innovation.
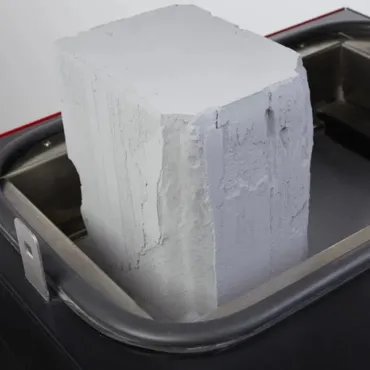

Materials
Glass Fiber
PA1101
PA2200
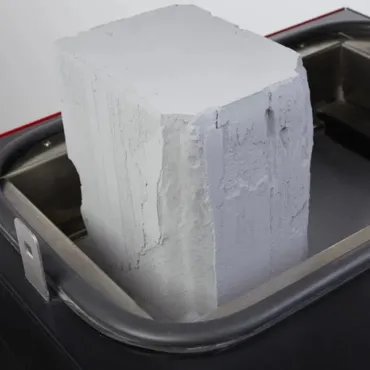

Process Flow :
Preparation:
The process begins with digital design data, which is prepared using Computer-Aided Design (CAD) software. The digital model is then sliced into thin layers, generating a series of cross-sectional data.
Material Handling:
A powdered material, typically a polymer or a metal, is loaded into the SLS 3D printer's build chamber. The powder is evenly spread across a build platform, forming a thin layer.
Laser Sintering:
A high-powered laser scans the cross-sectional data onto the powdered material, selectively melting and fusing the particles together. The laser's energy causes the powdered material to solidify, creating a solid layer of the object being printed.
Layer-by-Layer Building:
After each layer is sintered, the build platform moves down, and a fresh layer of powder is spread on top. The process repeats until the entire object is formed, layer by layer.
Cooling and Post-Processing
Once the printing is complete, the object is left to cool inside the printer. Afterward, excess powder is removed manually or using specialized equipment. Depending on the requirements, additional post-processing steps like polishing, dyeing, or surface treatment may be performed.
Advantages :
Design Freedom:
SLS enables the creation of highly complex geometries, including intricate internal structures and moving parts, without the need for assembly or additional tooling.
Versatility of Materials:
SLS can work with a wide range of materials, including polymers, metals, ceramics, and composites, allowing for the production of parts with diverse properties.
Cost-Efficiency:
As SLS does not require moulds or tooling, it eliminates the need for expensive and time-consuming manufacturing setups. This reduces production costs, especially for small batch sizes or customized products.
Time Savings:
SLS technology allows for rapid prototyping and quick iterations during the design process, accelerating product development cycles and reducing time-to-market.
Innovative Additive Manufacturing Solutions by RIFTWAY SOLUTIONS
On-Demand manufacturing offers industries flexibility, cost reduction, customization, sustainability and simplifying the supply chain